An asbestos survey is a structured inspection to locate and assess asbestos-containing materials (ACMs); an asbestos test is a laboratory analysis that identifies the fibre type and concentration.
The Control of Asbestos Regulations 2012 (CAR2012) define surveys as a duty to identify and manage risks, while testing confirms asbestos presence post-sampling. Surveys rely on visual inspection and sampling protocols, whereas testing provides definitive confirmation using microscopy.
Together, they form a compliance chain where the asbestos survey scopes risk, and the test validates material identity.
When Are These Asbestos Service Required
An asbestos survey is required before refurbishment or demolition as part of the duty to manage non-domestic premises or during property purchases. Specific materials suspected of containing asbestos or subsequent removal works necessitate testing to ensure air cleanliness.
For example, a homeowner planning a loft extension needs a refurbishment survey, while a landlord clearing textured coating from a hallway ceiling may only require targeted asbestos testing to confirm clearance. Each case depends on regulatory triggers and intended property use.
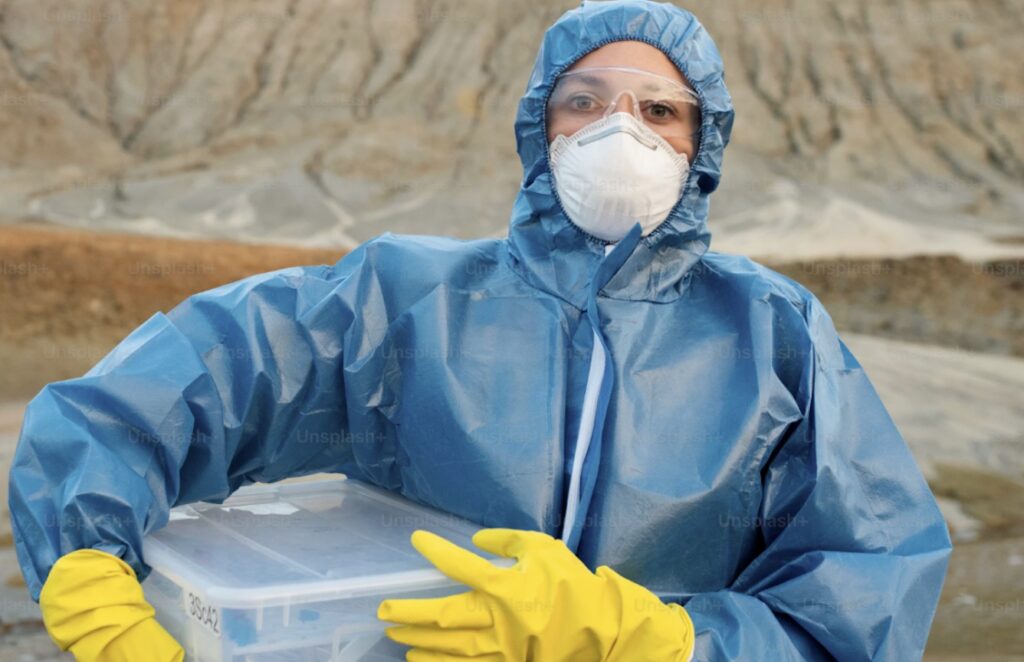
Asbestos Survey Types and Objectives
An asbestos screening survey identifies obvious ACMs through minimal sampling and visual checks—ideal for rapid, low-cost risk flagging.
A management survey assesses and risk-rates ACMs in a non-intrusive manner to create a live register for ongoing use. A refurbishment and demolition asbestos survey involves intrusive access and full sampling, required by law before any works.
A pre-purchase asbestos survey blends these aims to inform buyers or lenders. Deliverables range from risk registers to full compliance reports, with time on site from 1 to 3 days.
Asbestos Testing Methods and Protocols
Bulk asbestos sampling and polarised light microscopy (PLM) involve collecting small material pieces using UKAS-accredited methods to detect the presence of asbestos. Where asbestos fibre types are mixed or barely visible, scanning electron microscopy (SEM) or transmission electron microscopy (TEM) provide enhanced resolution.
Air monitoring assesses asbestos fibre concentrations through static or personal sampling, with clearance certificates being issued if the levels meet legal thresholds. Each process requires strict chain-of-custody, PPE protocols, and accreditation to maintain asbestos sample integrity and legal validity.
On-Site Asbestos Process Comparison
Asbestos surveyors begin with a scope meeting, followed by room-by-room visual inspection, selective sampling, and friability scoring.
Asbestos testers collect samples, secure them in tamper-proof containers, transport them under custody, then submit for lab QA/QC before issuing results.
The following table breaks down the differences between the two approaches:
Step | Survey | Testing |
---|---|---|
Planning | Site scoping | Sampling protocol |
Execution | Visual inspection & sampling | Targeted sample collection |
Post-process | Report with register | Lab analysis and certification |
Responsible Party | Surveyor (UKAS/ARCA/UKATA) | Lab technician (UKAS) |
Asbestos Report Contents and Interpretation
Asbestos reports are structured to meet compliance, clarity, and actionability requirements, including:
- Executive summary – A concise overview of findings, key risks, and recommended actions.
- Location maps – Visual floorplans showing exact ACM locations across surveyed areas.
- ACM photographs – Clear images documenting each identified or suspected asbestos material.
- Risk matrix with coded actions – Colour-coded table assessing material condition and urgency of response.
- ACM register – A formal log required under CAR2012, listing materials, condition, and management notes.
- Testing certificates – Lab-issued documents detailing sample IDs, test methods (PLM, SEM), fibre types/percentages, and UKAS accreditation stamps.
Interpreting asbestos reports involves checking location risk ratings (low to high) and ensuring clearance levels align with <0.01 fibres/cm³ standards as defined by HSE.
Asbestos Use-Case Decision Tree
Use an asbestos survey when a comprehensive risk profile is needed across a property—especially before refurbishment or for compliance with duty-to-manage regulations. Choose testing when you need to confirm if a specific material is asbestos or for post-removal air clearance.
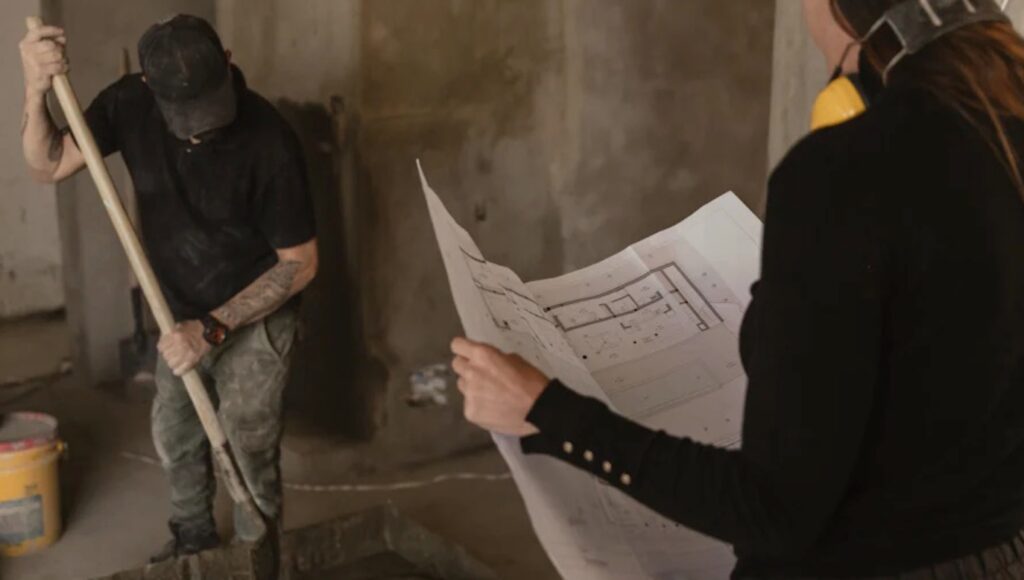
Some core decision ideas include:
- If full-building risk assessment → Survey
- If confirming one material or air quality → Testing
Asbestos surveys may require 10–50+ samples depending on size, while asbestos testing can target 1–3 specific materials.
Asbestos Survey Cost
Asbestos surveys cost £300–£1,200 depending on property size and scope, with on-site time between a few hours and 2 days. Asbestos reports are usually delivered within 3–7 working days.
Asbestos testing costs £50–£100 per sample, with results in 3–5 days. Expect disruption during intrusive works, such as access restrictions and signage during these testings. Grouping tests during an asbestos survey can lower costs and reduce repeat visits.
Common Pitfalls & Best Practices For Managing Asbestos Surveys and Tests
Common pitfalls in asbestos management include attempting DIY sampling, which poses serious exposure risks and almost always leads to regulatory non-compliance. It’s crucial to ensure that asbestos samples are taken from representative areas to avoid false negatives or missed materials.
Maintaining a documented chain of custody from collection to laboratory submission protects the legal validity of your results.
Poor coordination between asbestos surveyors and contractors can cause costly delays through repeat site visits, so aligning schedules from the outset is essential. Always follow HSE’s Approved Code of Practice (ACOP) to stay within legal duties regarding managing asbestos.